Stage 5 - Casting
In the cast shop, the plaster moulds were filled with slip. Moisture from the slip was absorbed by the plaster which would form a skin of clay in the mould. After an appropriate time, the cast would reach the desired thickness and the remaining slip in the mould would be run off and reclaimed.
The majority of production used a vitreous china slip but in later years a fine fireclay slip was also used for some products. Given its low firing distortion qualities, it was particularly useful for countertop basins where a precise fit was required.
Until the late 70’s individual moulds were cast on simple wooden benches. Although this method continued, the majority of production began to be converted to bank (or battery) units allowing all moulds to be cast simultaneously rather than singly or in pairs. The units were of steel construction with moulds fitted to trolleys allowing the moulds to be opened more easily. Other designs of bench were also developed to suit different products. A typical bench might contain 32 Closets, 51 Cisterns or 80 Basins.
The number of moulds a caster would work on would depend on the complexity and mix of the product. Typically the numbers might be around 30 for a closet, 80 for basins, or up to 150 for pedestals and cisterns.
A typical casting time would be around 1 hour but would vary depending on factors including mould age, temperature, and slip density. Following run-off, the cast would be left in the mould to harden sufficiently before the mould was opened and it was freed with the assistance of compressed air and removed.
The caster would work on the piece removing seams, punching any holes required for function or fittings, before sponging to a good finish. The caster would also stamp the date and his number onto the cast. This was later replaced by a barcode transfer which was used to record information as the piece passed through each process. The temperature in the cast shop would be raised overnight to dry both the cast and the mould. The following morning the cast would be checked, put onto a truck, and loaded to a dryer for a further day.
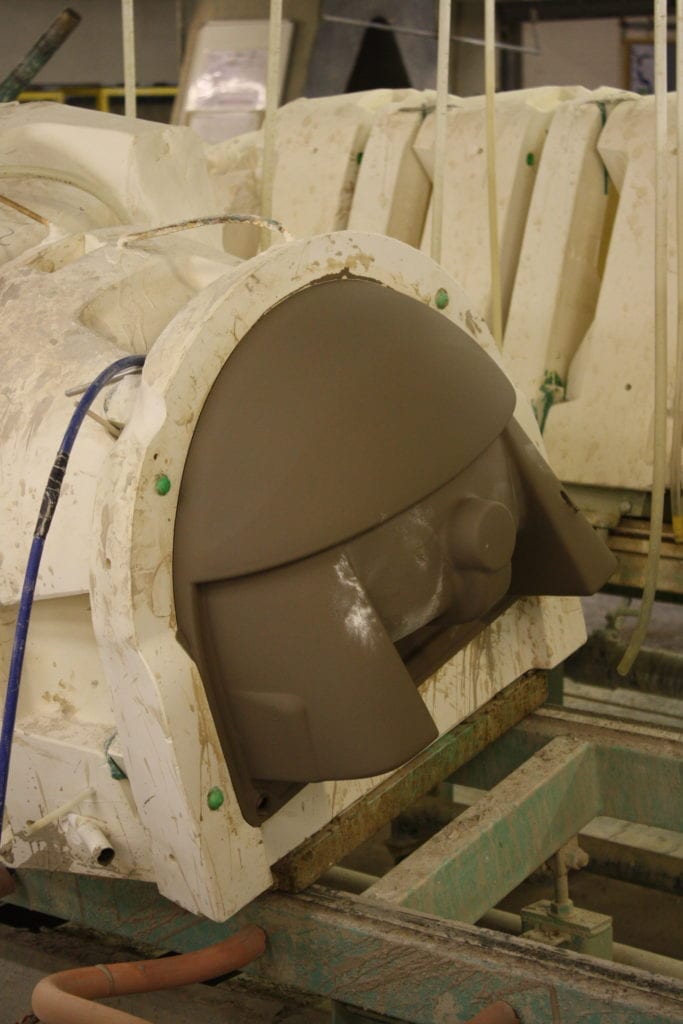